ONLINE MONITORING SYSTEM
FOR TOOL BREAK
ONLINE MONITORING
SYSTEM FOR TOOL BREAK
To Know When the Tool Breaks or Will Break
During the machining process, due to certain factors such as unreasonable tool path, unstable cutting force, uneven workpiece material, etc., tool break is very easy to occur, especially for small-diameter tools in high-speed machining. However, due to the influence of small tool size, small amount of cutting, cutting fluid used, etc., it cannot be found in time after the tool is broken, which affects the subsequent processing flow and wastes a lot of processing time, especially for semi-finishing or finishing.
To this end, JINGDIAO has developed an "Online Monitoring System for Tool Break", monitoring the tool status and accurately recording the tool break time, which makes it impossible to judge whether the tool is broken in real time during long processing, and assists in improving production efficiency and reducing processing risks.
Convenient Installation Design
Without Professional Requirements
Convenient Installation Design Without Professional Requirements
The system is mainly composed of three parts: high-frequency vibration sensor, vibration monitoring module and data monitoring software. By installing vibration sensors on key parts in any affected area by machining vibration, such as spindles, workpiece and fixtures, the vibration “characteristic signals” collected to monitoring software can be utilized to distinguish whether the current tool is broken. If a tool break occurs, the machine tool can send an alarm signal containing the tool break time and notify the operator to change the tool in time.
24-Hour Online Monitoring During Machining Process
The biggest highlight of the system is the 24-hour online monitoring of the tool status during the machining process, to reduce the processing risk caused by the tool broken tool. In addition, it also has other monitoring functions, such as abnormal collision and tool abnormal wear. It is convenient for operators to quickly identify and locate processing risk issues, and technologists to optimize processes, which achieves comprehensive machining process control, and improves production continuity and efficiency.
Real-Time Online Monitoring of Tool Status
Unlike the general use of the tool set to detect the tool status offline, this system has a 24-hour non-stop online monitoring of the tool status in real time to determine whether it is in normal cutting or a broken tool has occurred.
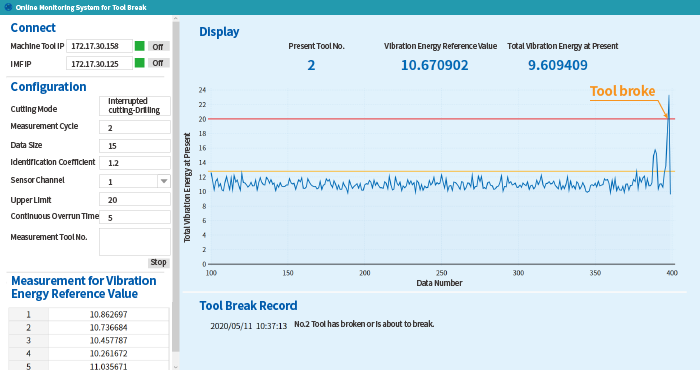
Tool break monitoring interface of Φ0.25mm bit
Online Monitoring of Tool Abnormal Wear
The "characteristic signal" data of the tool vibration provided by this system can be used as a reference curve to judge whether the tool wears. In some scenarios, it can be used as a prediction curve for abnormal tool wear and tool break, to provide data basis for production personnel to prepare and exchange tools.
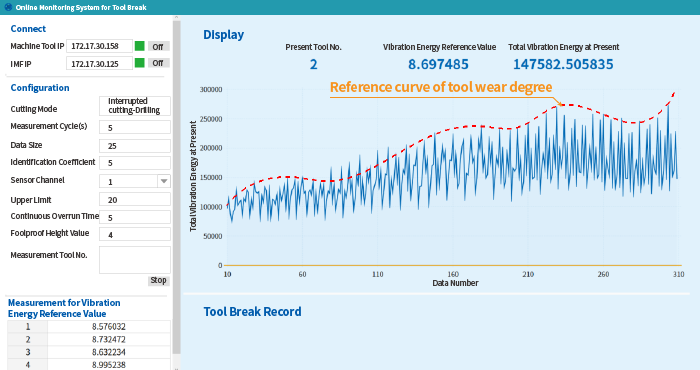
Reference curve of tool wear degree
Online Monitoring of Abnormal Collision
By setting the collision warning value, the abnormal collision can be detected accurately and effectively that occurs during the machining process. An alarm will remind the production personnel to check the tool status in time to avoid greater safety risks.
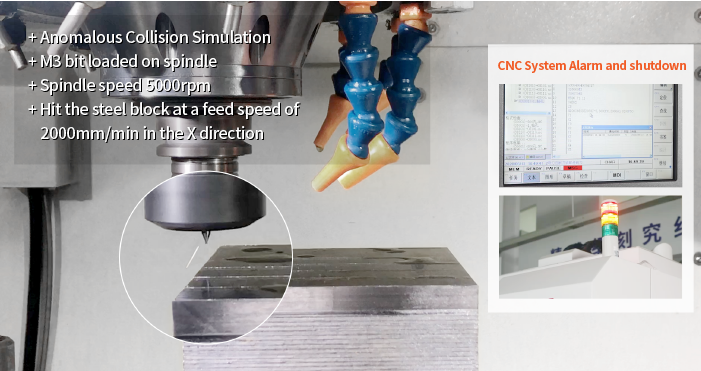
Simulation experiment of an abnormal collision
Recognition Ability of “μm" Cutting Amount
Based on the characteristics of the vibration signal, the system uses the method of comparing and sorting the full frequency band “characteristic signals” before and after cutting, to monitor the tool status in real time. Therefore, the system has high sensitivity and rapid response, and can monitor the tool status with "μm" cutting amount, particularly suitable for difficult monitoring situations such as long-term high-speed finishing of small tools.
Milling
It can monitor whether the tool is worn or broken, when the minimum cutting amount is 2μm.
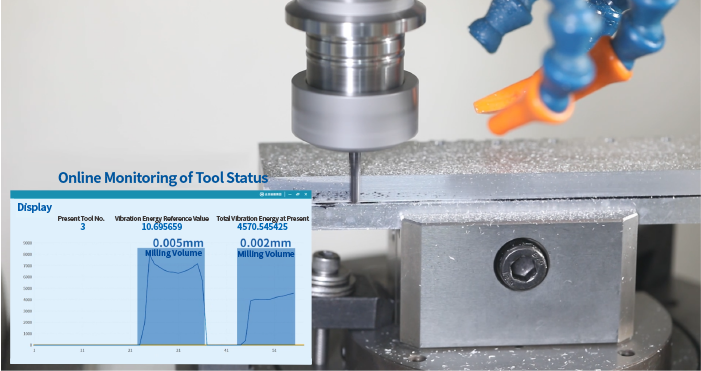
Online Monitoring of Tool Status--Milling
Grinding
It can monitor whether the grinding head or grinding wheel is in the normal state, when the minimum grinding amount is 1μm.
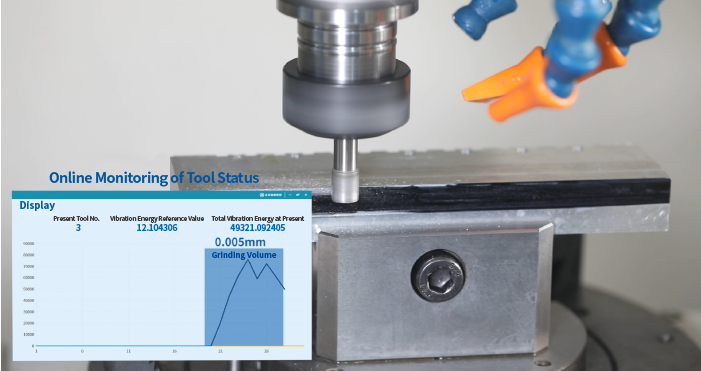
Online Monitoring of Tool Status--Grinding
Drilling
It can monitor whether the bit is broken, whose minimum diameter is 0.2mm.
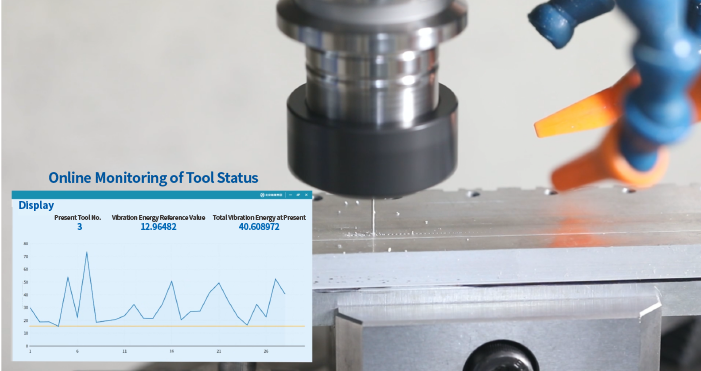
Online Monitoring of Tool Status--Drilling
Only Four Steps to Use the Monitoring System
JINGDIAO “Online Monitoring System for Tool Break” is a simple and easy-to-use monitoring platform, which only needs four steps for operation, to handle the real-time monitoring of the broken tool during the CNC machining.
Parameter Settings
Set important parameters such as cutting method and upper limit
Online Monitoring
Online monitoring of "characteristic signal" data of the tool vibration
Tool Break Judgment
If the curve exceeds the upper limit, the tool is about to break or has broken.
System Alarm
If the tool is about to break or has broken, the CNC system will alarm in time and stop processing immediately.